
The Principles of Laser Welding
Laser welding utilizes the excellent directional and high power density characteristics of a laser beam to work. Through an optical system, the laser beam is focused on a very small area, creating a highly concentrated heat source in a very short period. This process melts the material at the welding point, forming a solidified weld spot and seam.
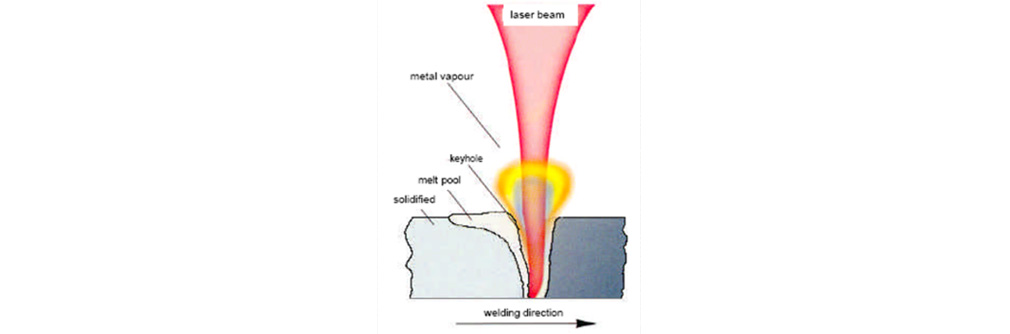
· Laser welding is generally divided into conduction welding and deep penetration welding.
· A laser power density of 105~106w/cm2 results in laser conduction welding.
· A laser power density of 105~106w/cm2 results in laser deep penetration welding.
The Characteristics of Laser Welding
Compared to other welding methods, laser welding possesses the following characteristics:
· Focused energy, high welding efficiency, high processing precision, and a large depth-to-width ratio of the weld seam.
· Low heat input, small heat-affected zone, minimal residual stress, and low deformation of the workpiece.
· Non-contact welding, fiber optic transmission, good accessibility, and high level of automation.
· Flexible joint design, saving raw materials.
· Welding energy can be precisely controlled, ensuring stable welding results and a good welding appearance.
Welding of Steel and its Alloys
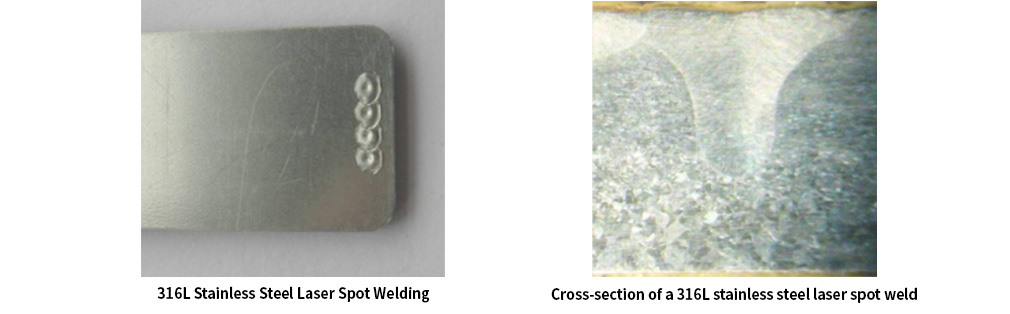
· Stainless steel can achieve good welding results using a standard square wave.
· When designing welded structures, try to keep the weld points away from non-metallic substances as much as possible.
· To meet strength and appearance requirements, it is advisable to reserve sufficient welding area and workpiece thickness.
· During welding, it is essential to ensure the cleanliness of the workpiece and the dryness of the environment.
Welding of Aluminum and its Alloys
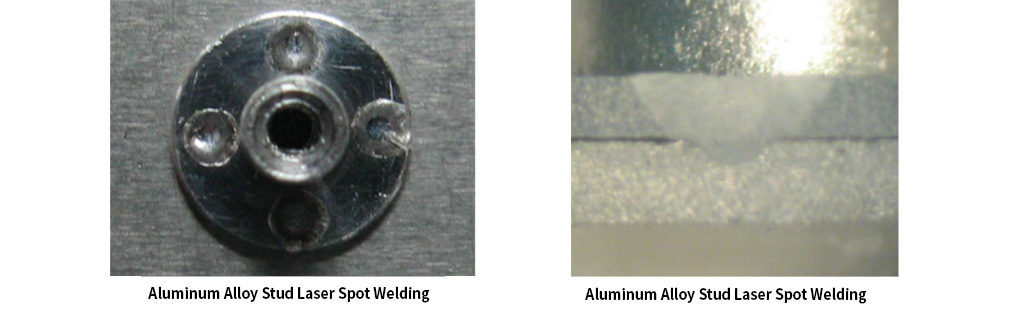
· Aluminum alloy materials have a high reflectivity; therefore, a high laser peak power is needed during welding.
· Cracks are prone to occur during pulse spot welding, affecting the welding strength.
· The material composition is prone to segregation, leading to splattering. It is advisable to choose high-quality raw materials.
· Generally, using a large spot size and long pulse width can achieve better welding results.
Welding of Copper and its Alloys
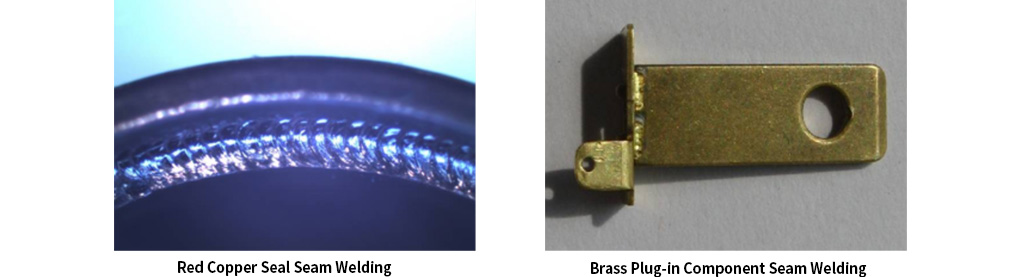
· Copper materials have a higher reflectivity compared to aluminum alloys, requiring higher peak laser power for welding. The laser head needs to be tilted at a certain angle.
· For certain copper alloys, such as brass and bronze, the welding difficulty is increased due to the influence of alloy elements. Attention should be paid to the selection of welding process parameters.
Dissimilar Metal Welding
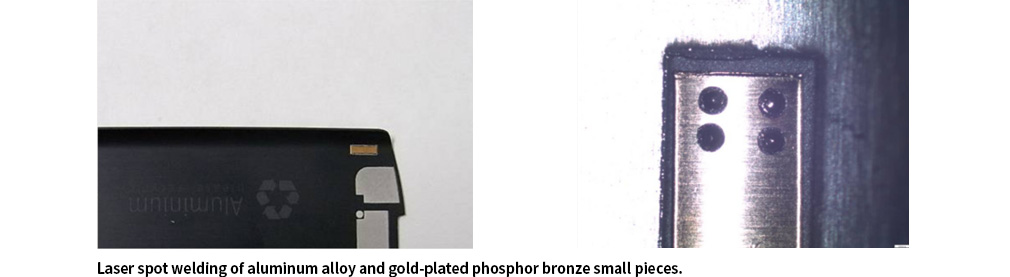
· Can a solid solution be formed.
· Is there a significant difference in electronegativity between dissimilar metals.
· Other influencing factors.
Whether dissimilar metals can form high-quality welding joints mainly depends on the physical properties, chemical properties, chemical composition, and process measures of the metals to be welded. This is typically considered from the following aspects:
· Whether a solid solution can be formed depends on whether dissimilar metals can mutually dissolve in the liquid and solid states. Only when they can dissolve in each other indefinitely, a strong and solid weld joint can be formed. Generally, a significant solubility, or even unlimited solubility, is achievable only when the atomic radius difference between the two metals is less than approximately 14% to 15%.
· Whether there is a significant difference in electronegativity between dissimilar metals is also crucial. The greater the difference, the stronger their chemical affinity, which tends to lead to the formation of compounds rather than solid solutions. As a result, the solubility of the solid solution that is formed is reduced, and the strength of the weld joint is also lower.
· Additionally, the welding of dissimilar metals is greatly affected by properties such as melting points, coefficients of thermal expansion, thermal conductivities, specific heats, oxidizability, and reflectivity of the materials involved. The greater the difference in these physical properties, the more challenging it is to weld, and the weaker the strength of the resulting weld joint tends to be.
· Usually, laser welding of dissimilar metal materials such as steel with copper, aluminum, and nickel, as well as copper with nickel, exhibits good weldability, leading to satisfactory welding quality.
Laser welding finds extensive applications across various sectors, including but not limited to the following areas:
1: Dissimilar Metal Welding
Laser welding is widely employed in manufacturing industries such as automotive, aerospace, electronics, and mechanical engineering. It is used for welding components and assembling structures, enhancing production efficiency and product quality.
2: Medical Devices
In the manufacturing of medical devices, laser welding is utilized for connecting and assembling small, precision components, ensuring high-quality products while avoiding excessive heat impact on materials.
3: Electronics
Due to its high precision and low heat input, laser welding is widely applied in the manufacturing of electronic devices, including circuit board welding and microelectronic components.
4: Aerospace
Laser welding is used in the aerospace sector for manufacturing aircraft and aerospace components, enabling lightweight design and high-strength connections.
5: Energy Sector
In the energy industry, laser welding is employed for manufacturing solar panels, nuclear power equipment, and other components related to energy production.
6: Jewelry and Watchmaking
Given its adaptability to fine and intricate structures, laser welding is often used in the manufacturing of jewelry and watches for connecting and repairing delicate components.
7: Automotive Industry
In automotive manufacturing, laser welding is employed for connecting automotive components, improving welding efficiency, and enhancing product quality.
Overall, the high precision, speed, and versatility of laser welding make it widely applicable in manufacturing and production fields.
由用户整理投稿发布,不代表本站观点及立场,仅供交流学习之用,如涉及版权等问题,请随时联系我们(yangmei@bjjcz.com),我们将在第一时间给予处理。
Post time: Jan-17-2024